Beläggningsmetoderna för fotoresist är i allmänhet uppdelade i spinnbeläggning, doppbeläggning och rullbeläggning, bland vilka spinnbeläggning är den vanligast använda. Genom spinnbeläggning droppas fotoresist på substratet och substratet kan roteras med hög hastighet för att erhålla en fotoresistfilm. Efter det kan en fast film erhållas genom att värma den på en varm platta. Spinnbeläggning är lämplig för beläggning från ultratunna filmer (ca 20nm) till tjocka filmer på ca 100um. Dess egenskaper är god likformighet, enhetlig filmtjocklek mellan wafers, få defekter etc. och en film med hög beläggningsprestanda kan erhållas.
Spinnbeläggningsprocess
Under spinnbeläggning bestämmer substratets huvudsakliga rotationshastighet fotoresistens filmtjocklek. Förhållandet mellan rotationshastigheten och filmtjockleken är som följer:
Spin=kTn
I formeln är Spin rotationshastigheten; T är filmtjockleken; k och n är konstanter.
Faktorer som påverkar spinnbeläggningsprocessen
Även om filmtjockleken bestäms av huvudrotationshastigheten, är den också relaterad till rumstemperatur, fuktighet, fotoresistviskositet och fotoresisttyp. Jämförelse av olika typer av fotoresistbeläggningskurvor visas i figur 1.
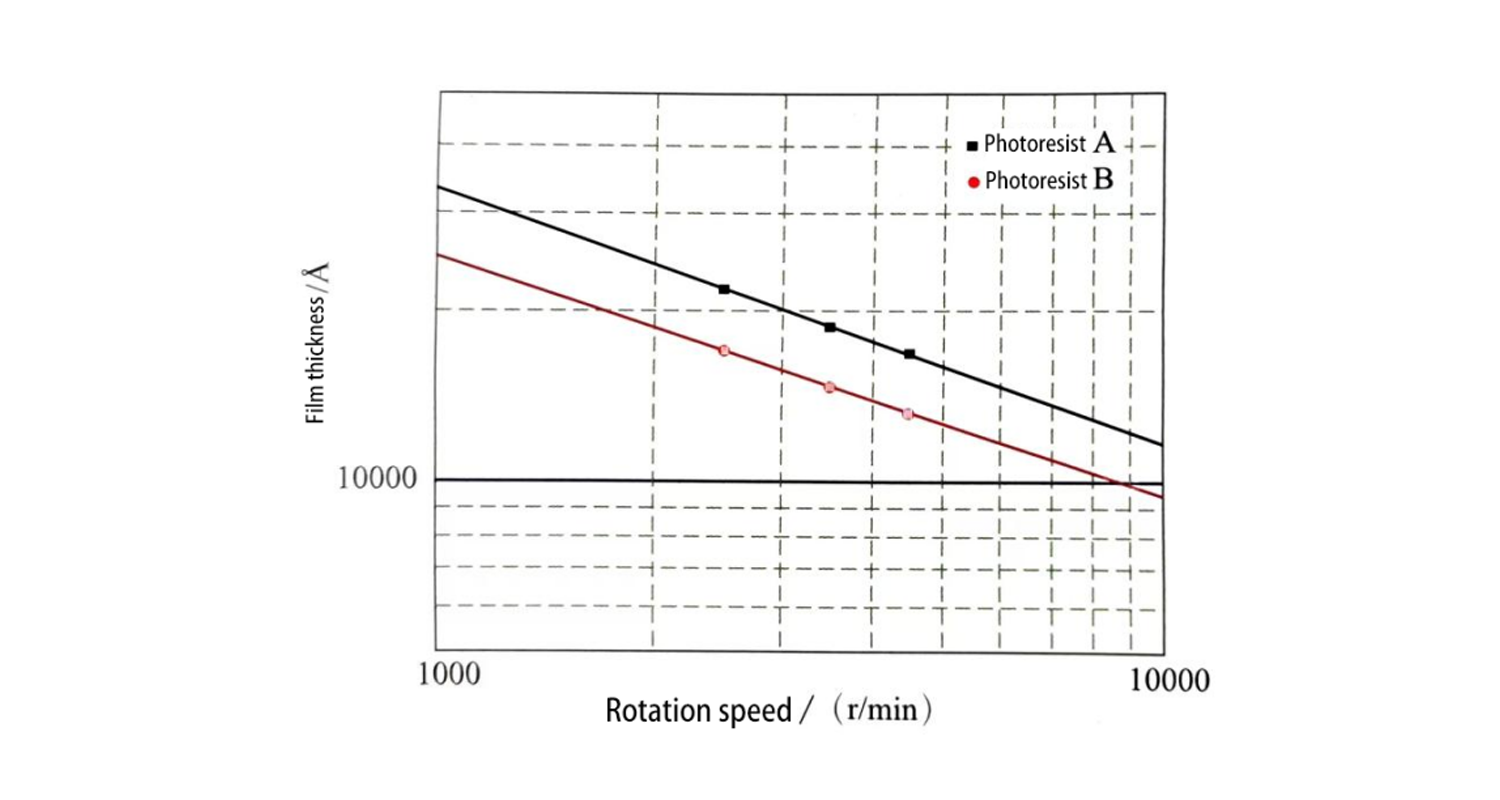
Figur 1: Jämförelse av olika typer av fotoresistbeläggningskurvor
Inverkan av huvudrotationstiden
Ju kortare huvudrotationstiden är, desto tjockare filmtjocklek. När huvudrotationstiden ökas desto tunnare blir filmen. När den överstiger 20s förblir filmtjockleken nästan oförändrad. Därför väljs huvudrotationstiden vanligtvis till att vara mer än 20 sekunder. Förhållandet mellan huvudrotationstiden och filmtjockleken visas i figur 2.
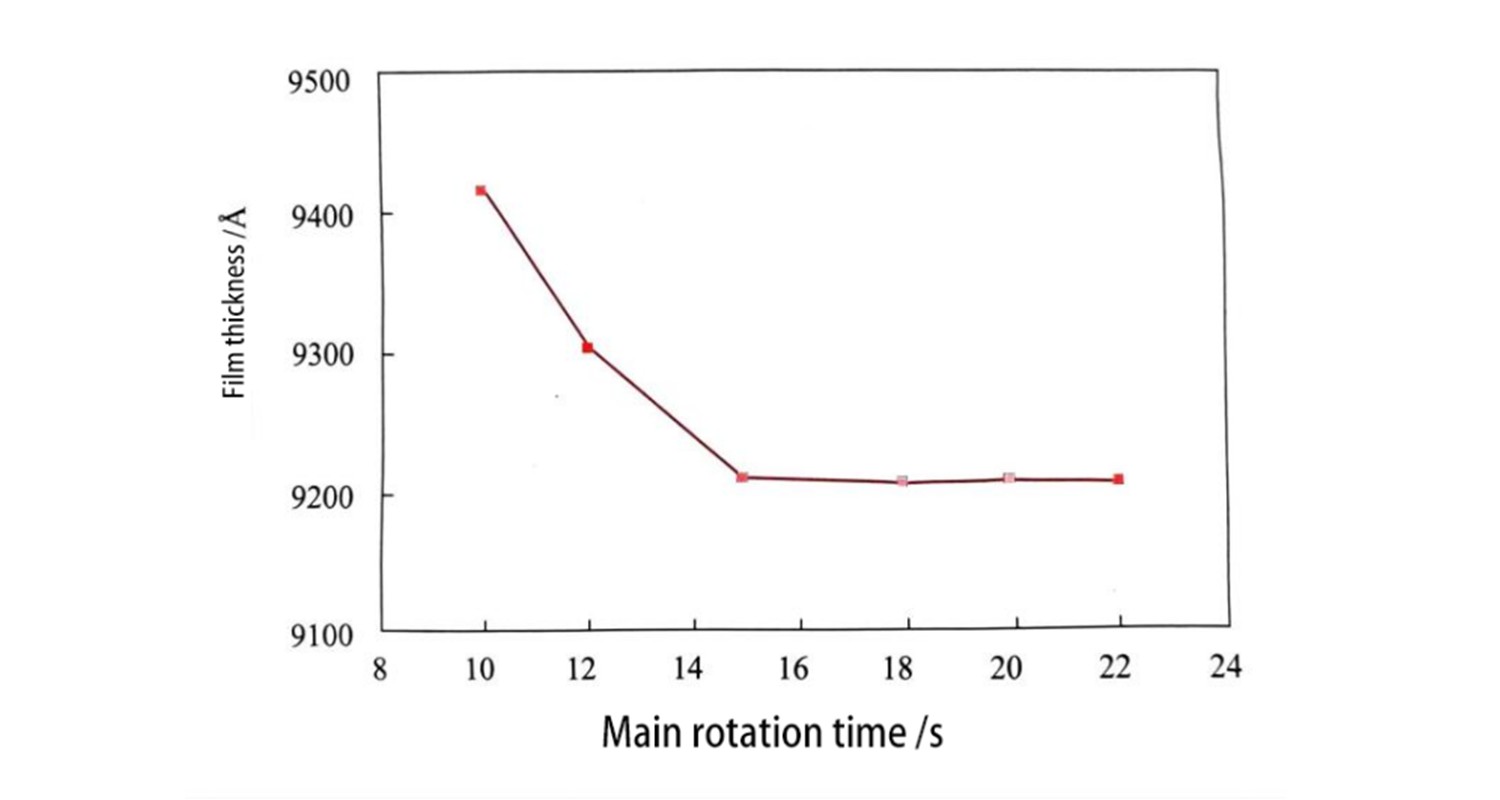
Figur 2: Samband mellan huvudrotationstid och filmtjocklek
När fotoresisten droppas på substratet, även om den efterföljande huvudrotationshastigheten är densamma, kommer rotationshastigheten för substratet under droppningen att påverka den slutliga filmtjockleken. Tjockleken på fotoresistfilmen ökar med ökningen av substratets rotationshastighet under droppningen, vilket beror på inverkan av lösningsmedelsavdunstning när fotoresisten viks ut efter droppning. Figur 3 visar förhållandet mellan filmtjockleken och huvudrotationshastigheten vid olika substratrotationshastigheter under fotoresistdroppningen. Det kan ses från figuren att med ökningen av rotationshastigheten för det droppande substratet ändras filmtjockleken snabbare, och skillnaden är mer uppenbar i området med lägre huvudrotationshastighet.
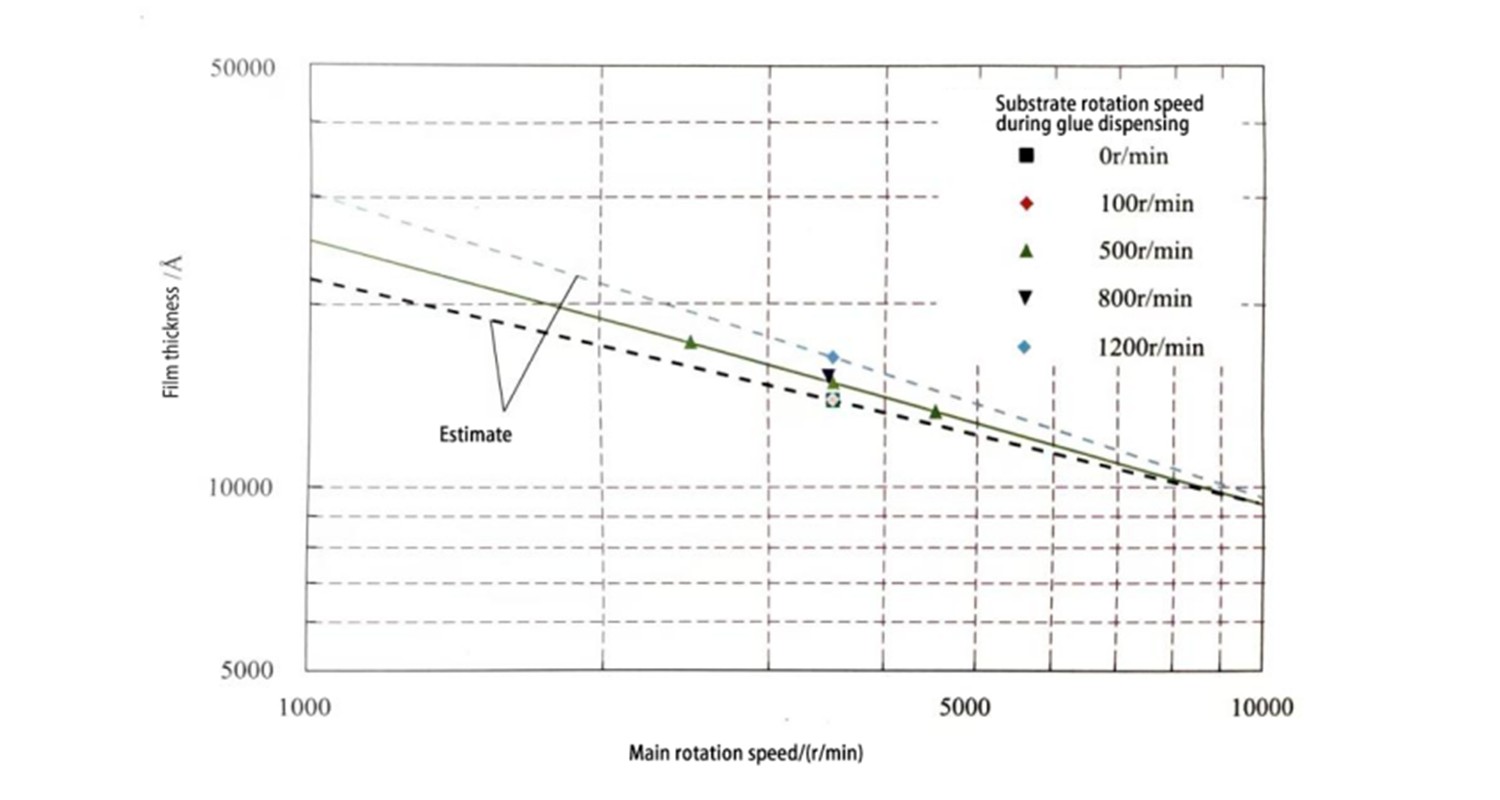
Figur 3: Förhållandet mellan filmtjocklek och huvudrotationshastighet vid olika substratrotationshastigheter under fotoresistdispensering
Effekt av fukt under beläggning
När luftfuktigheten minskar ökar filmtjockleken, eftersom minskningen av luftfuktigheten främjar avdunstning av lösningsmedlet. Filmtjockleksfördelningen förändras dock inte nämnvärt. Figur 4 visar förhållandet mellan fuktighet och filmtjockleksfördelning under beläggning.
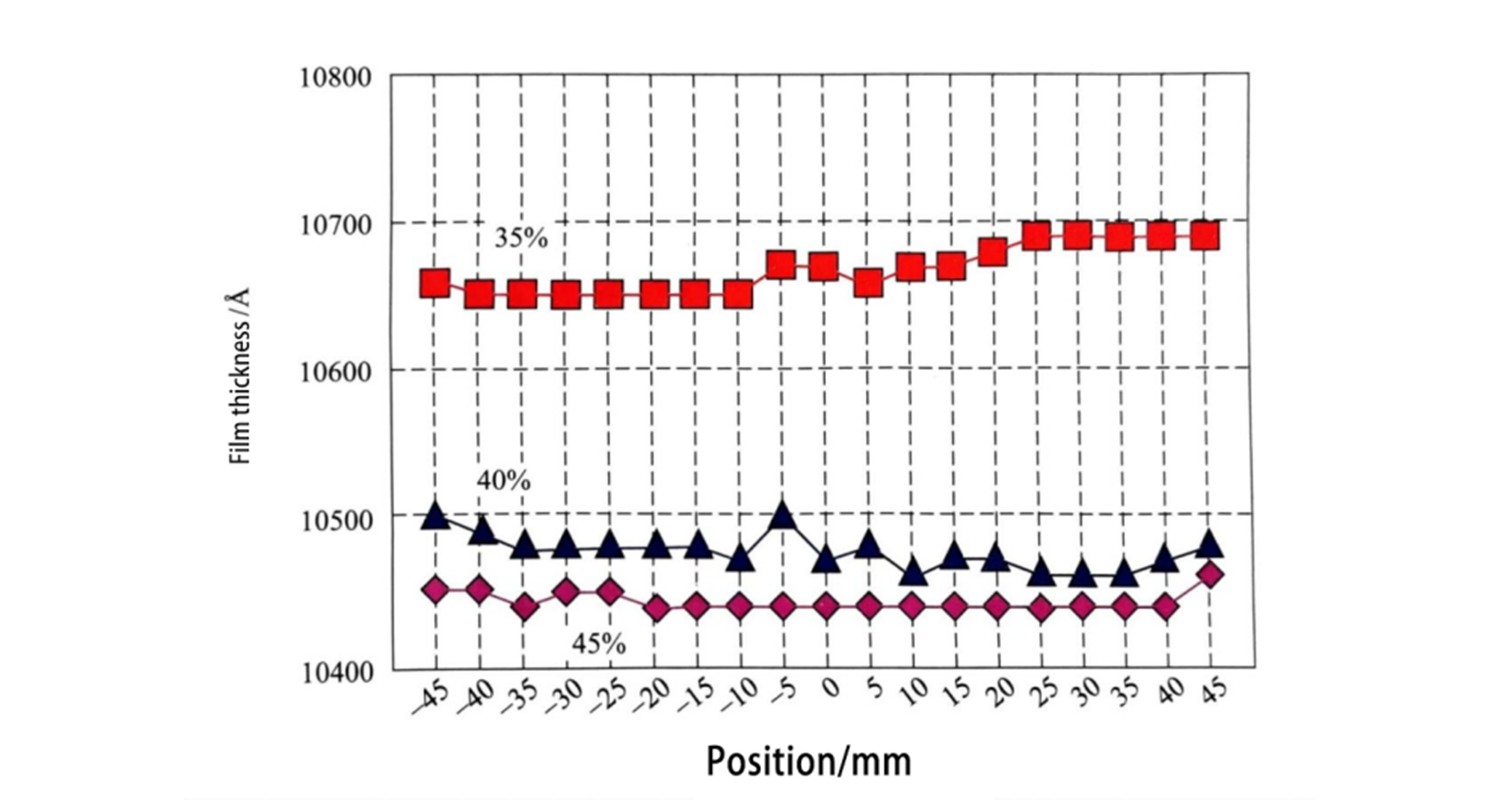
Figur 4: Samband mellan fuktighet och filmtjockleksfördelning under beläggning
Effekt av temperatur under beläggning
När inomhustemperaturen stiger ökar filmtjockleken. Det kan ses från figur 5 att fördelningen av fotoresistfilmens tjocklek ändras från konvex till konkav. Kurvan i figuren visar också att den högsta enhetligheten erhålls när inomhustemperaturen är 26°C och fotoresisttemperaturen är 21°C.
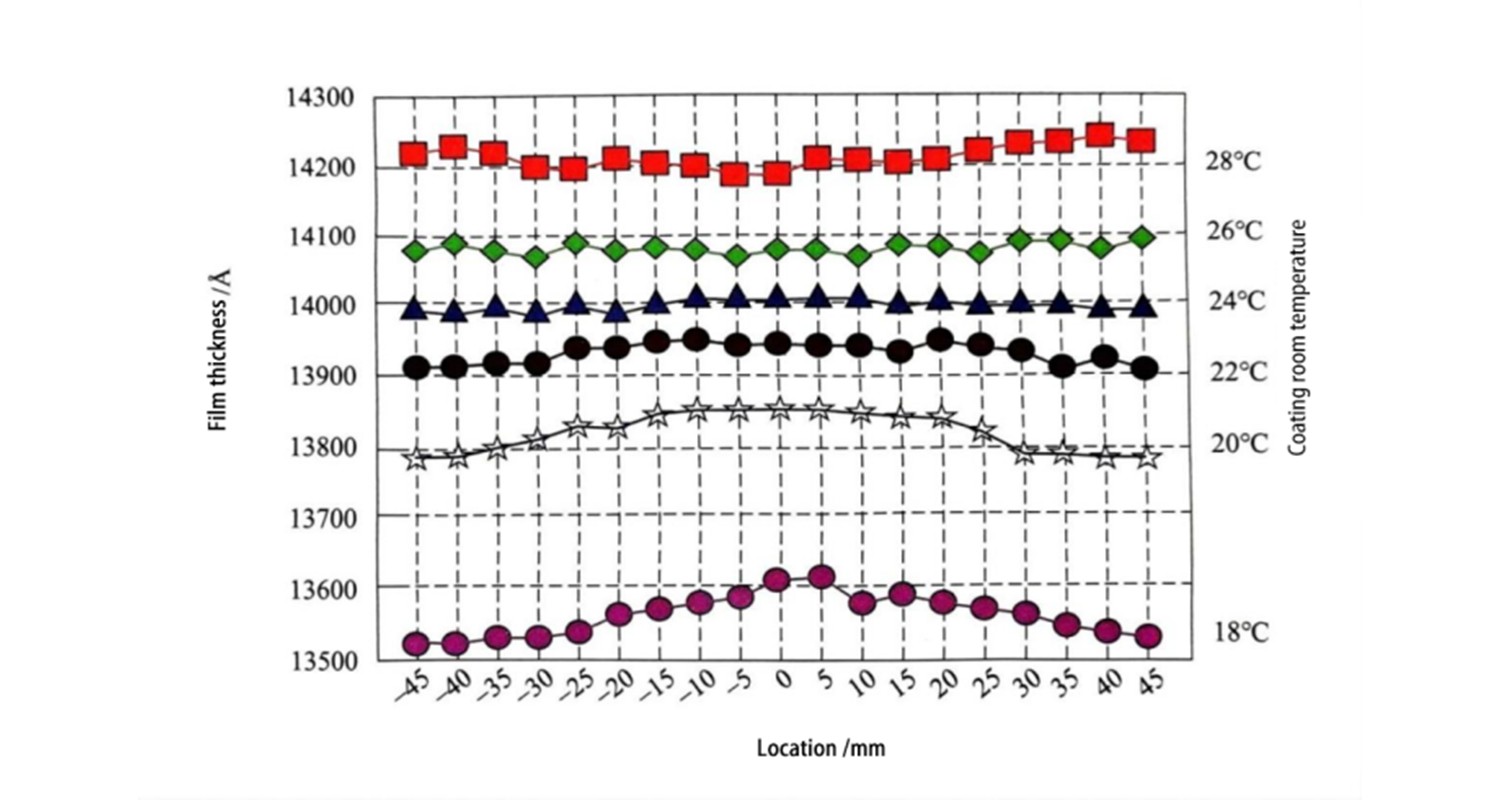
Figur 5: Samband mellan temperatur och filmtjockleksfördelning under beläggning
Effekt av avgashastighet under beläggning
Figur 6 visar förhållandet mellan avgashastighet och filmtjockleksfördelning. I frånvaro av avgaser visar det att mitten av skivan tenderar att tjockna. En ökning av avgashastigheten kommer att förbättra likformigheten, men om den höjs för mycket kommer likformigheten att minska. Det kan ses att det finns ett optimalt värde för avgashastigheten.
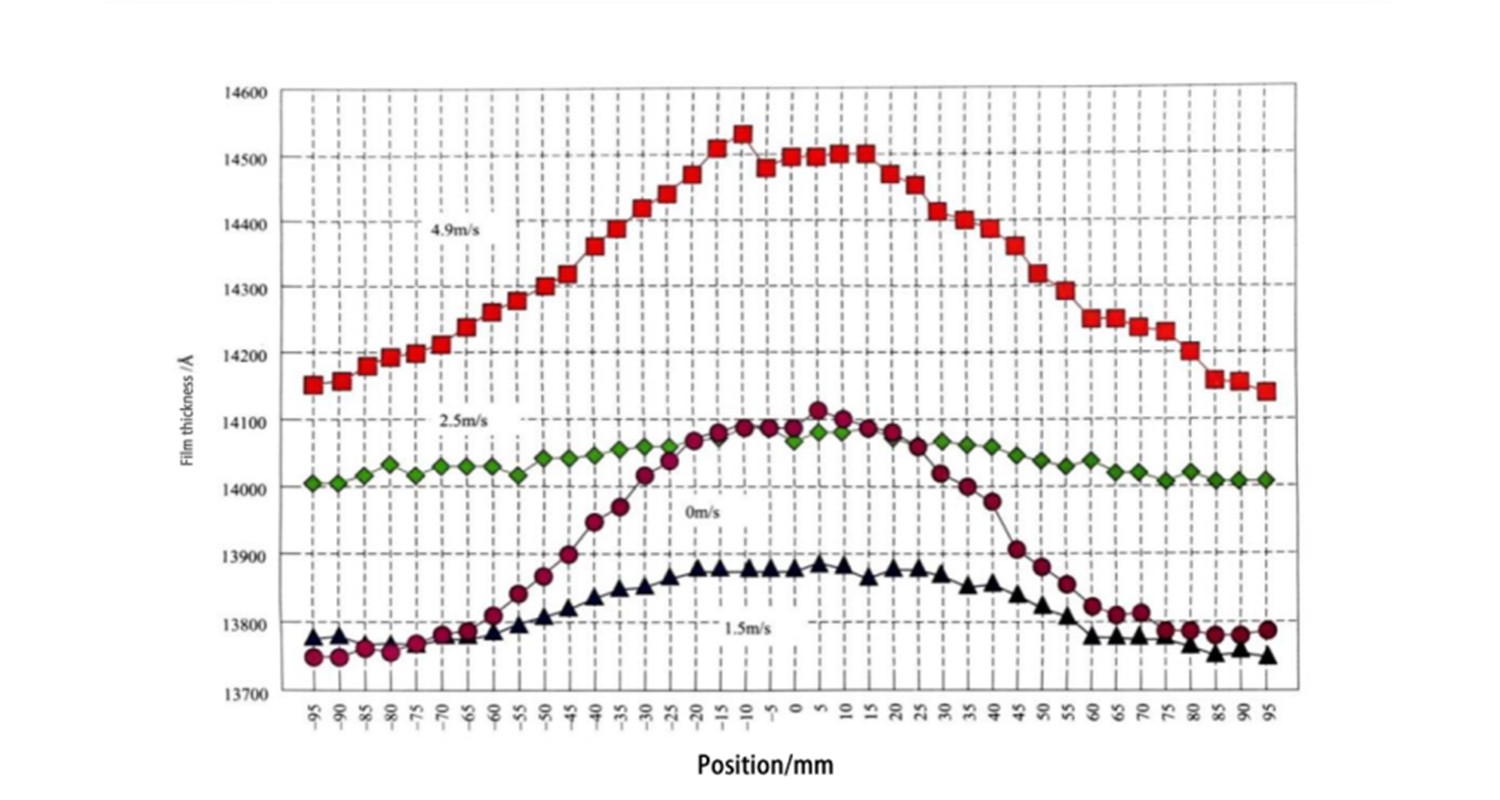
Figur 6: Samband mellan avgashastighet och filmtjockleksfördelning
HMDS behandling
För att göra fotoresisten mer beläggningsbar måste skivan behandlas med hexametyldisilazan (HMDS). Speciellt när fukt fästs på ytan av Si-oxidfilmen bildas silanol, vilket minskar vidhäftningen av fotoresisten. För att avlägsna fukt och sönderdela silanol, värms skivan vanligtvis till 100-120°C, och dimma HMDS introduceras för att orsaka en kemisk reaktion. Reaktionsmekanismen visas i figur 7. Genom HMDS-behandling blir den hydrofila ytan med liten kontaktvinkel en hydrofob yta med stor kontaktvinkel. Uppvärmning av skivan kan erhålla högre fotoresistvidhäftning.
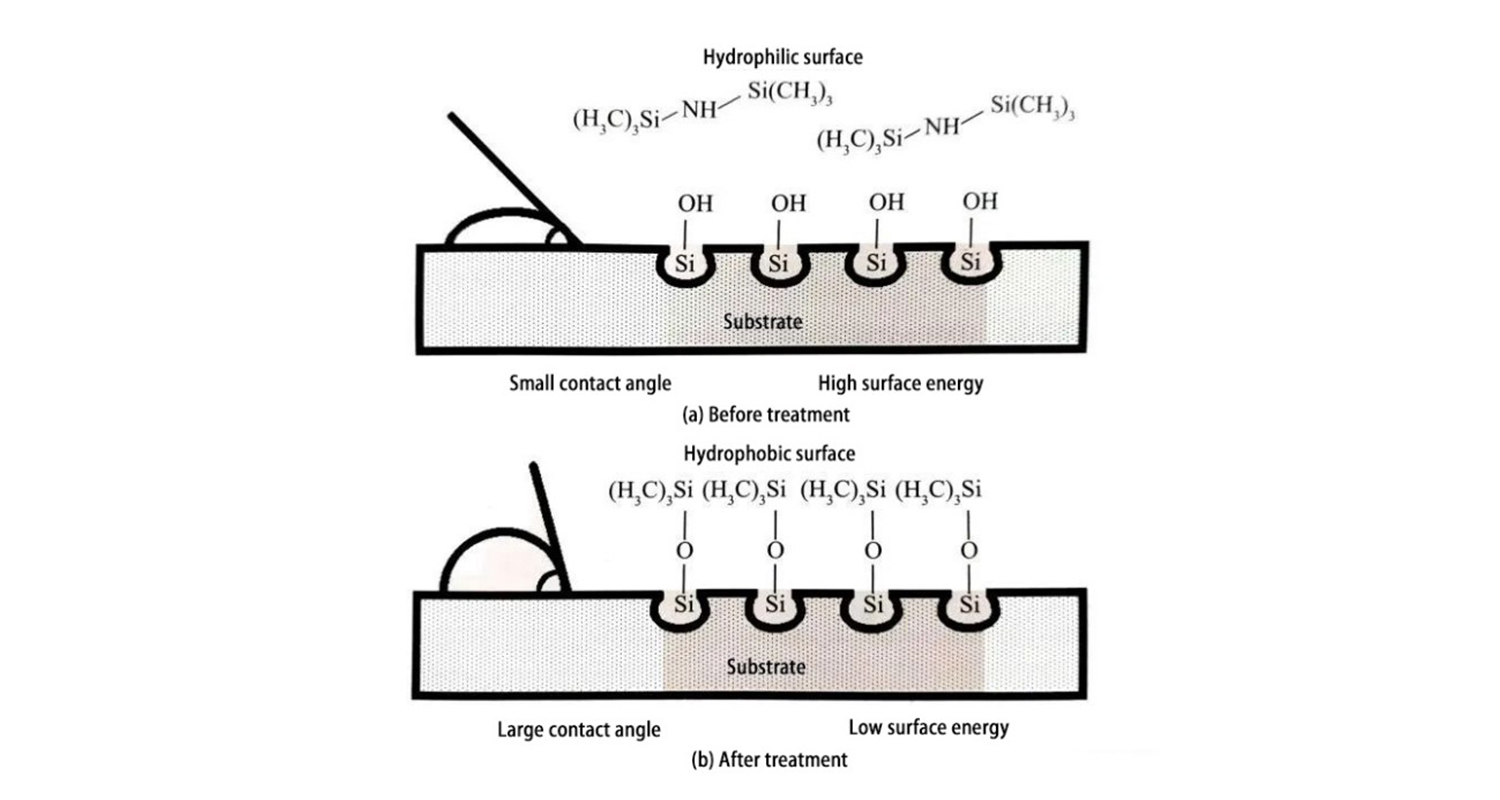
Figur 7: HMDS-reaktionsmekanism
Effekten av HMDS-behandling kan observeras genom att mäta kontaktvinkeln. Figur 8 visar förhållandet mellan HMDS-behandlingstid och kontaktvinkel (behandlingstemperatur 110°C). Substratet är Si, HMDS-behandlingstiden är längre än 1 min, kontaktvinkeln är större än 80° och behandlingseffekten är stabil. Figur 9 visar sambandet mellan HMDS-behandlingstemperatur och kontaktvinkel (behandlingstid 60s). När temperaturen överstiger 120℃ minskar kontaktvinkeln, vilket indikerar att HMDS sönderfaller på grund av värme. Därför utförs HMDS-behandling vanligtvis vid 100-110 ℃.
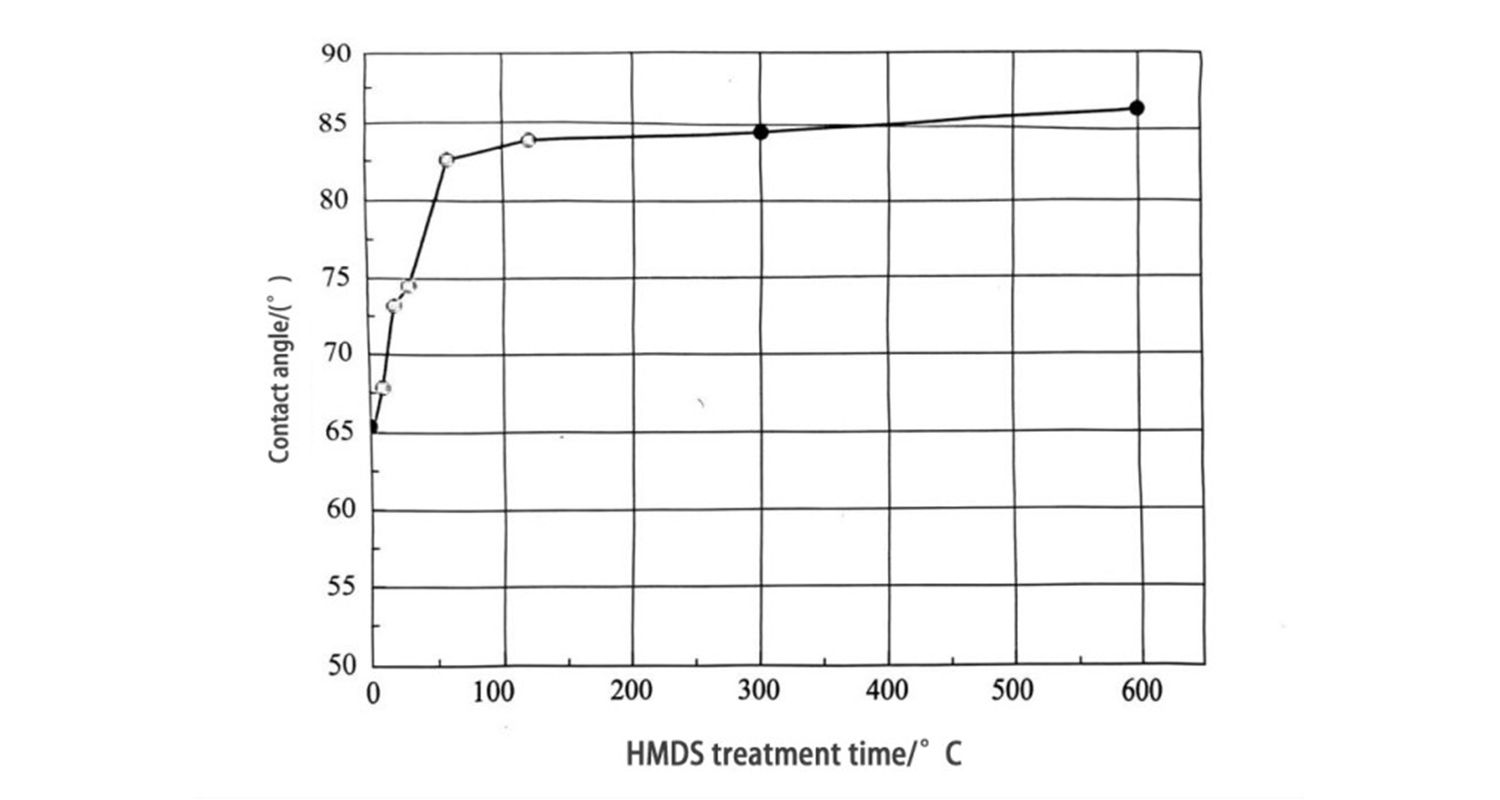
Figur 8: Samband mellan HMDS-behandlingstid
och kontaktvinkel (behandlingstemperatur 110 ℃)
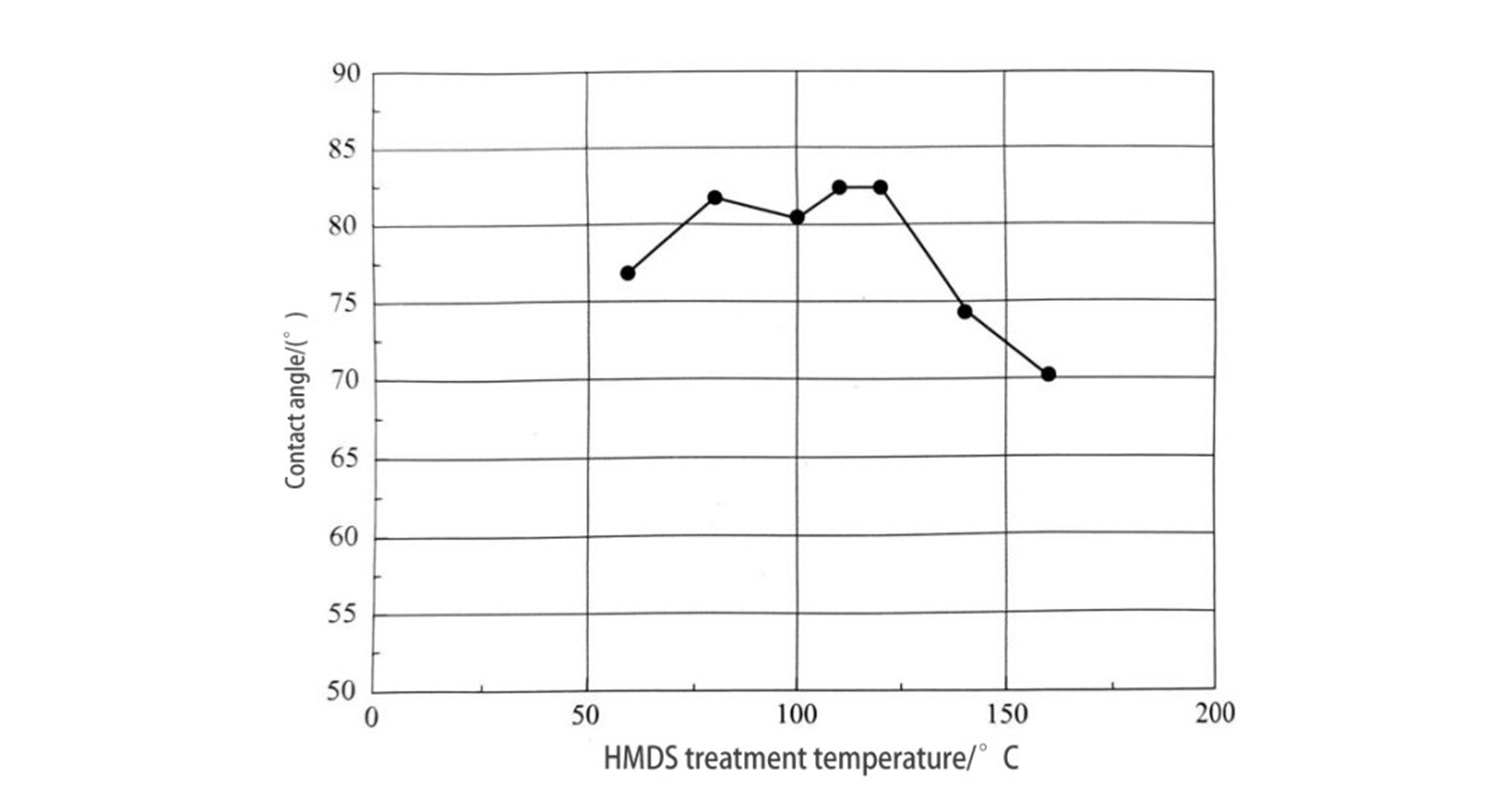
Figur 9: Samband mellan HMDS behandlingstemperatur och kontaktvinkel (behandlingstid 60s)
HMDS-behandling utförs på ett kiselsubstrat med en oxidfilm för att bilda ett fotoresistmönster. Oxidfilmen etsas sedan med fluorvätesyra med en buffert tillsatt, och det visar sig att efter HMDS-behandling kan fotoresistmönstret förhindras att falla av. Figur 10 visar effekten av HMDS-behandling (mönsterstorleken är 1um).
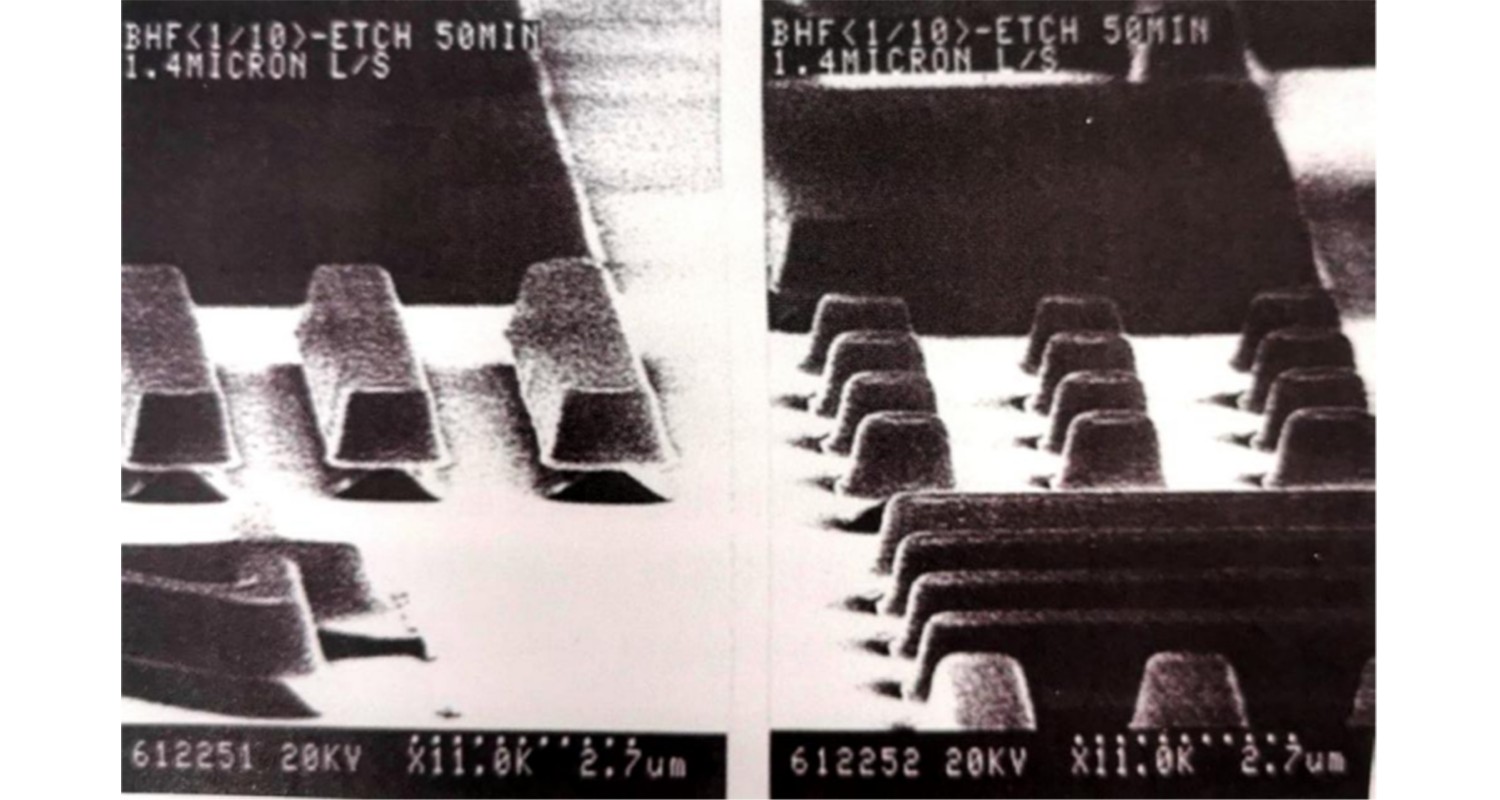
Figur 10: HMDS-behandlingseffekt (mönsterstorleken är 1um)
Förbakning
Vid samma rotationshastighet, ju högre förbakningstemperatur, desto mindre filmtjocklek, vilket indikerar att ju högre förbakningstemperatur, desto mer lösningsmedel avdunstar, vilket resulterar i en tunnare filmtjocklek. Figur 11 visar förhållandet mellan förgräddningstemperaturen och Dills A-parameter. A-parametern indikerar koncentrationen av det ljuskänsliga medlet. Som framgår av figuren, när förgräddningstemperaturen stiger till över 140°C, minskar A-parametern, vilket indikerar att det ljuskänsliga medlet sönderdelas vid en temperatur högre än denna. Figur 12 visar spektraltransmittansen vid olika förgräddningstemperaturer. Vid 160°C och 180°C kan en ökning av transmittansen observeras i våglängdsområdet 300-500 nm. Detta bekräftar att det ljuskänsliga medlet bakas och sönderdelas vid höga temperaturer. Förgräddningstemperaturen har ett optimalt värde, vilket bestäms av ljusegenskaper och känslighet.
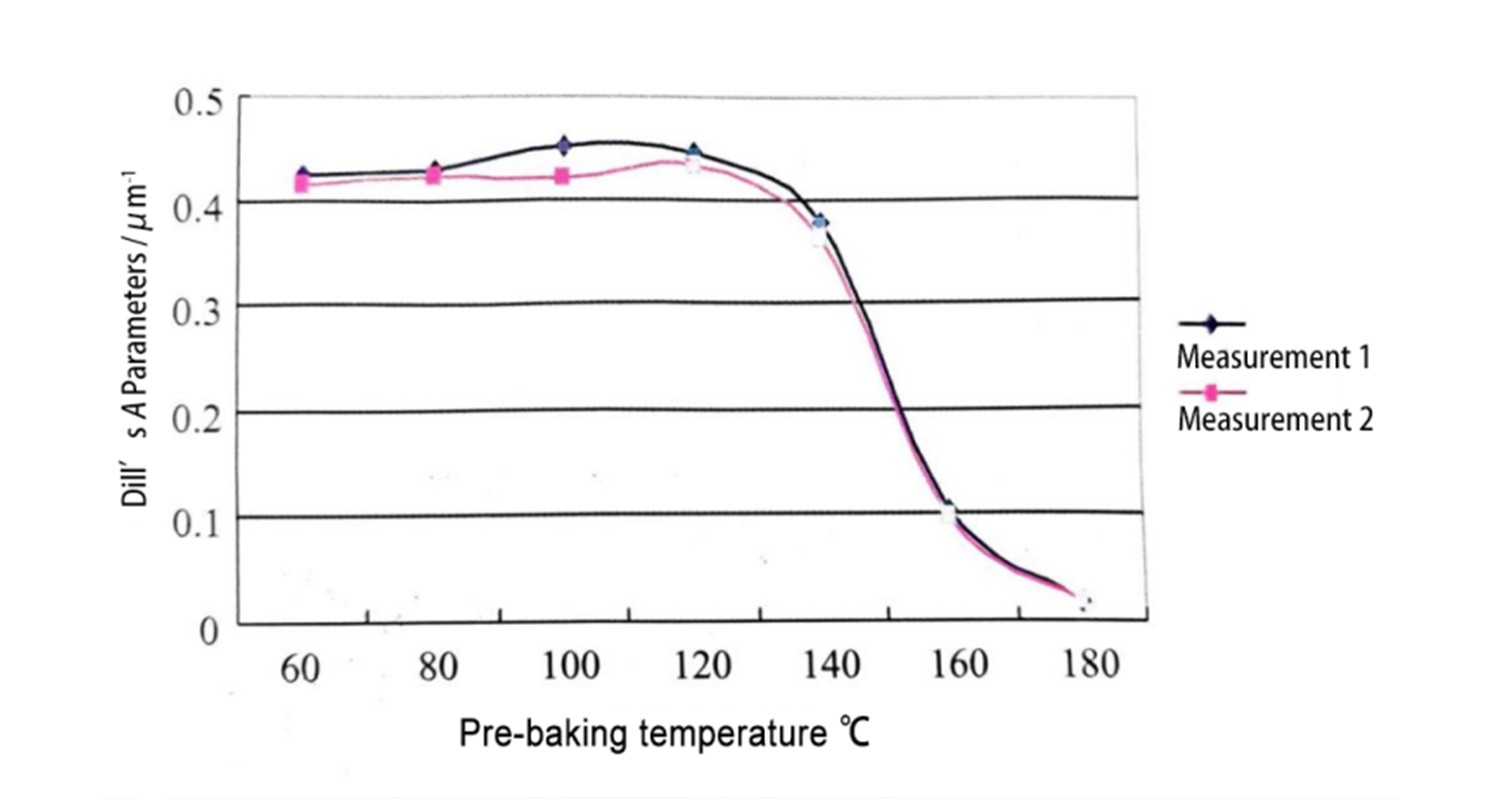
Figur 11: Samband mellan förgräddningstemperatur och Dills A-parameter
(uppmätt värde för OFPR-800/2)
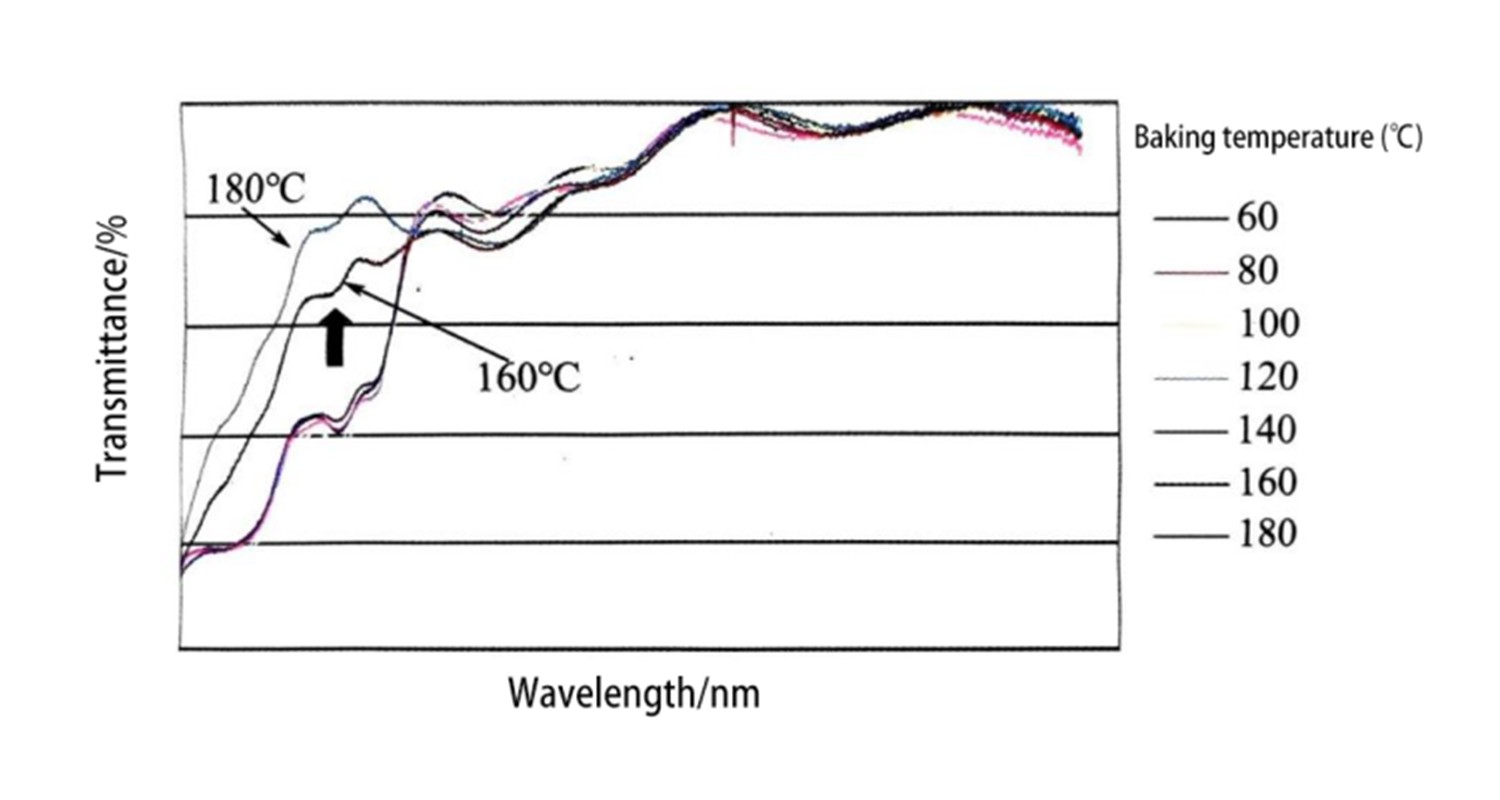
Figur 12: Spektral transmittans vid olika förgräddningstemperaturer
(OFPR-800, 1um filmtjocklek)
Kort sagt har spinnbeläggningsmetoden unika fördelar som exakt kontroll av filmtjocklek, hög kostnadsprestanda, milda processförhållanden och enkel drift, så den har betydande effekter för att minska föroreningar, spara energi och förbättra kostnadsprestanda. Under de senaste åren har spinnbeläggning fått allt större uppmärksamhet och dess tillämpning har gradvis spridit sig till olika områden.
Posttid: 2024-nov-27